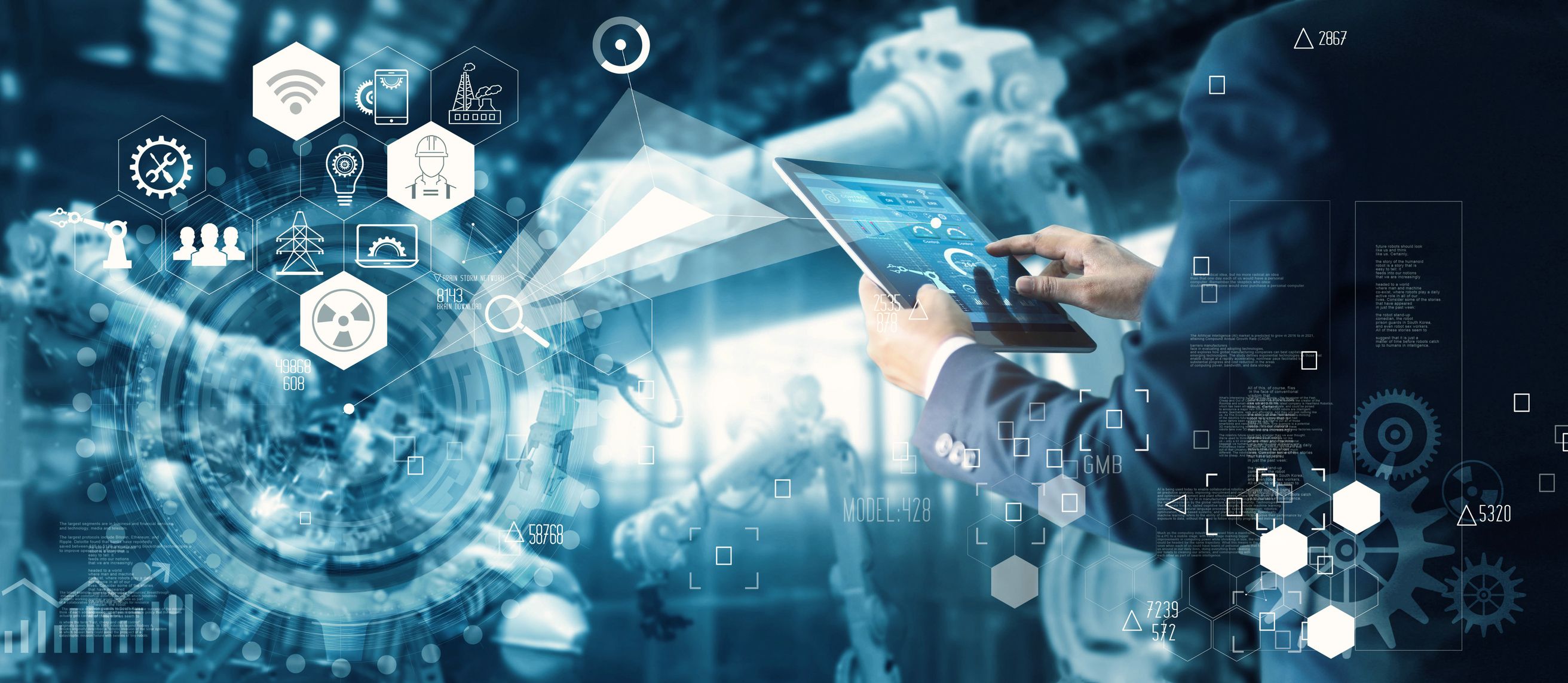
Hay conceptos que, cada cierto tiempo, se cuelan como tendencia monotemàtica en el ámbito económico. En los últimos años, la Industria 4.0 oposita a quedarse con esta posición. La llamada cuarta revolución industrial plantea la completa transformación digital de las empresas con la creación de fábricas inteligentes, en la que cada proceso productivo esté automatizado y conectado entre sí. Un concepto sencillo, que promete una reducción en los costes de fabricación de entre el 10% y el 40% -según quien haga el estudio-, pero que genera desazones entre muchos empresarios por la transformación física y conceptual que supone y por los costes que implica su implantación. La jornada Industria 4.0: la revolución digital aplicada en la fábrica, organizada por Pimec, ha servido para clarificar conceptos y derrocar mitos.
"Avanzar en conceptos de digitalización es más sencillo y menos costoso del que parece". Así se expresaba el director general de FESTO en España y Portugal, Xavier Segura, que asegura que se pueden conseguir grandes mejoras con pequeñas transformaciones. "El simple hecho de formar un equipo de 50 comerciales puede suponer organizar 50 viajes, reservar hoteles y todos los gastos derivados; digitalizar este único ámbito de la empresa a través de la formación virtual o mixta ya supone una reducción inmensa de dinero, a través de una inversión amortizable en un solo año y que se podrá aprovechar cada vez que entre una nueva persona".
Segura recomienda iniciar el despliegue 4.0 de las fábricas por etapas, a partir de las necesidades y los objetivos de cada empresa. "A veces los objetivos son tan simples como mejorar la calidad de nuestros productos, la flexibilidad o reducir un 40% el coste de producción. Un golpe los tengamos identificados podremos buscar las soluciones tecnológicas que nos ayuden a lograrlos". El empresario recuerda, a guisa de ejemplo, como el 40% de la inversión al captar nuevos clientes se produce en el seguimiento posterior a las visitas comerciales, y asegura que la utilización de aplicaciones de envío y seguimiento de las operaciones hace caer en picado este porcentaje. "La tecnología está a nuestra disposición; sólo necesitamos poner la idea".
Comparte la reflexión el director comercial y de marketing industrial de AEtech, Xevi Sagué, que recomienda a los empresarios preguntarse si la digitalización forma parte de su plan estratégico antes de empezar a invertir. "El que suele suceder es que el director general de una empresa viene a una charla como esta, coge a una persona de confianza dentro de la empresa y le adjudica 50.000 euros para que empiece un piloto en Industria 4.0. Esto no forma parte de la cultura empresarial y está condenado al fracaso".
Sagué considera que, para iniciar un proyecto de digitalización exitós hace falta "un desencadenante que traiga a adquirir el conocimiento necesario, a visualizar el beneficio que obtendremos y, finalmente, a impulsar la empresa introduciendo la digitalización en su estrategia".
Ahora bien, quién tiene que ser el impulsor de la digitalización de la empresa? Por jerarquía, la respuesta evidente es la dirección, pero la industria actual cada vez entiende menos de verticalidad. "Dentro de la empresa hay gente mucho más cercana en la tecnología y capaz de entender qué beneficios traerá la implementación de sistemas de inteligencia artificial que los directivos. Son ellos los que tienen que desplegar la Industria 4.0 dentro de su radio de actuación, hacer propuestas pequeñas y que se puedan implementar basadas en tres factores: "Qué soy, que quiero hacer y que puedo hacer", recomienda la responsable de desarrollo de negocio de tecnologías digitales de Eurecat, Lali Soler.
Necesidades formativas
El problema en la aplicación de la digitalización muchas veces no es de voluntad ni de estrategia, sino de carencia de formación. La distancia entre academia e industria es una queja histórica en el ámbito productivo que se ha acentuado con la aceleración del desarrollo tecnológico. "Las empresas vamos diez años por detrás de las tecnologías, pero es que las universidades van diez años atrasadas respecto a la industria. Hay que intervenir en los planes de estudio para formar profesionales según las necesidades de las compañías", reivindica el CEO de Infaimon, Salvador Giró.
A pesar de coincidir en el argumento, Soler reivindica una formación generalista como garantía de formar personas con capacidad para plantear y resolver problemas. "No vale de nada tener una plantilla de especialistas hipertecnològics si no contamos con mentalidades agregadores que piensen en como abordar un reto: la creación de una fábrica inteligente sólo es el final de un camino que se construiráa paso según las necesidades de la empresa".
El ROI de la digitalización industrial
Cómo en toda inversión, apostar por la Industria 4.0 sólo tiene sentido si hay un regreso. De nuevo, la clave para conseguirlo es insertar esta digitalización en la cultura y la estrategia de la empresa. "Incluir la digitalización en el plan estratégico quiere decir que hay unos beneficios cuantificables y cualitativos asociados que tenemos previstos", explica Sagué, que aporta su propia experiencia a AEtech. "Después de más de 40 proyectos de implementación digital integral en sistemas productivos hemos detectado pilares de beneficio: la mejora operacional, con la eliminación de tiempos muertos; la reducción de costes, con procesos más eficientes y la caída de horas dedicadas a ciertas tareas; el mantenimiento de la calidad a través de la repetición; y la generación de información estratégica en tiempo real, que es el elemento de más valor en la actualidad".
Sagué asegura que con la aplicación de la Industria 4.0 todos estos indicadores mejoran entre un 15% y un 25%, pero avisa sobre la necesidad de mantener una inversión en el tiempo para garantizar los resultados. "Detrás de una inversión tecnológica hay de haber una partida prevista en sistemas de mejora continua y un equipo multidisciplinario de todas las áreas estratégicas de la empresa que detecte nuevas necesidades en los sistemas productivos".
Los expertos coinciden: la Industria 4.0 reclama una inversión continuada. A cambio, promete beneficios y la creación de empresas constantemente actualizadas.